A bright sunny morning in Kutch. Indigo-dyed fabrics were spread out on the ground in the open fields. Looking at how raw the view looked, I expected that something coarse was in the making. My imagination further got validated when I learnt that every piece of fabric goes through multiple steps of washing, printing, dyeing, boiling and re-washing to finally become Ajrakh (we all know how old clothes look like is what I imagined in my head). But I was amazingly surprised when I looked at the final products – all vibrant, pleasing to the eyes and soft against the skin. That’s the beauty of crafts.
- Contents:
- What is Ajrakh?
- Where is Ajrakh practised predominantly?
- Origin and history
- The meticulous Ajrakh Process:
- Q&A with an Ajrakh artisan to know the unknown about Ajrakh
- Micro level challenges faced by an Ajrakh artisan
- Macro level challenges faced by the community
WHAT IS AJRAKH: It is a unique block-printing craft technique which derives its name from the Arabic word ‘Azrak’ meaning ‘blue’. Local practitioners also resemble Ajrakh as “aaj-rakh” (keep it today) as, after each of the sixteen processes, one needs to spread out and dry the fabric.
WHERE IS AJRAKH PRACTISED PREDOMINANTLY: It is practised in the Kutch district in Gujarat and Barmer in Rajasthan. It is also practised in parts of Sindh in Pakistan.
ORIGIN AND HISTORY: Ajrakh is believed to have existed in the Sindh region since the Indus Valley civilization (wao!). It was introduced in India about 400 yrs ago by the Khatri community who then moved and settled in Kutch and in Barmer regions of India. Traditional Ajrakh craftsmen i.e. the Katri community have been into this art for generations.
THE METICULOUS AJRAKH PROCESS: Sixteen to twenty-three exhaustive and laborious steps are involved in the making. These steps are broadly categorised into washing, printing, dying and drying which are repeated almost in order each time to achieve the final product.
First, the fabric is washed and soaked in a solution of myrobalan which is a natural mordant that helps the fabric to absorb the dyes. Then, a resist paste made of clay, gum, and lime is used to block out specific areas of the fabric, creating intricate geometric and floral patterns that are characteristic of Ajrakh.
The fabric is then dyed in the desired colour using natural plant and vegetable dyes. After this, the resist paste is washed off, and the fabric is printed with another layer of resist paste and dyed in another shade of natural colour.
This process is repeated several times, with different resist pastes and dyes, to create multiple layers of intricate patterns and colours.
Finally, the fabric is washed and dried, revealing the stunning finished product. The entire process of creating an Ajrakh textile can take several weeks or even months to complete, depending on the complexity of the design.
SNEAK PEEK INTO THE LIFE OF AN AJRAKH ARTISAN – MICRO AND MACRO CHALLENGES
We went through a lot of articles and videos which were already available on the web but it felt like something was missing. Nothing really spoke about the life and challenges of an artisan, and how one can identify authentic block-printed Ajrakh products. So when we planned our meet with an Ajrakh artisan from the Khatri community in Kutch to get answers to all our questions.
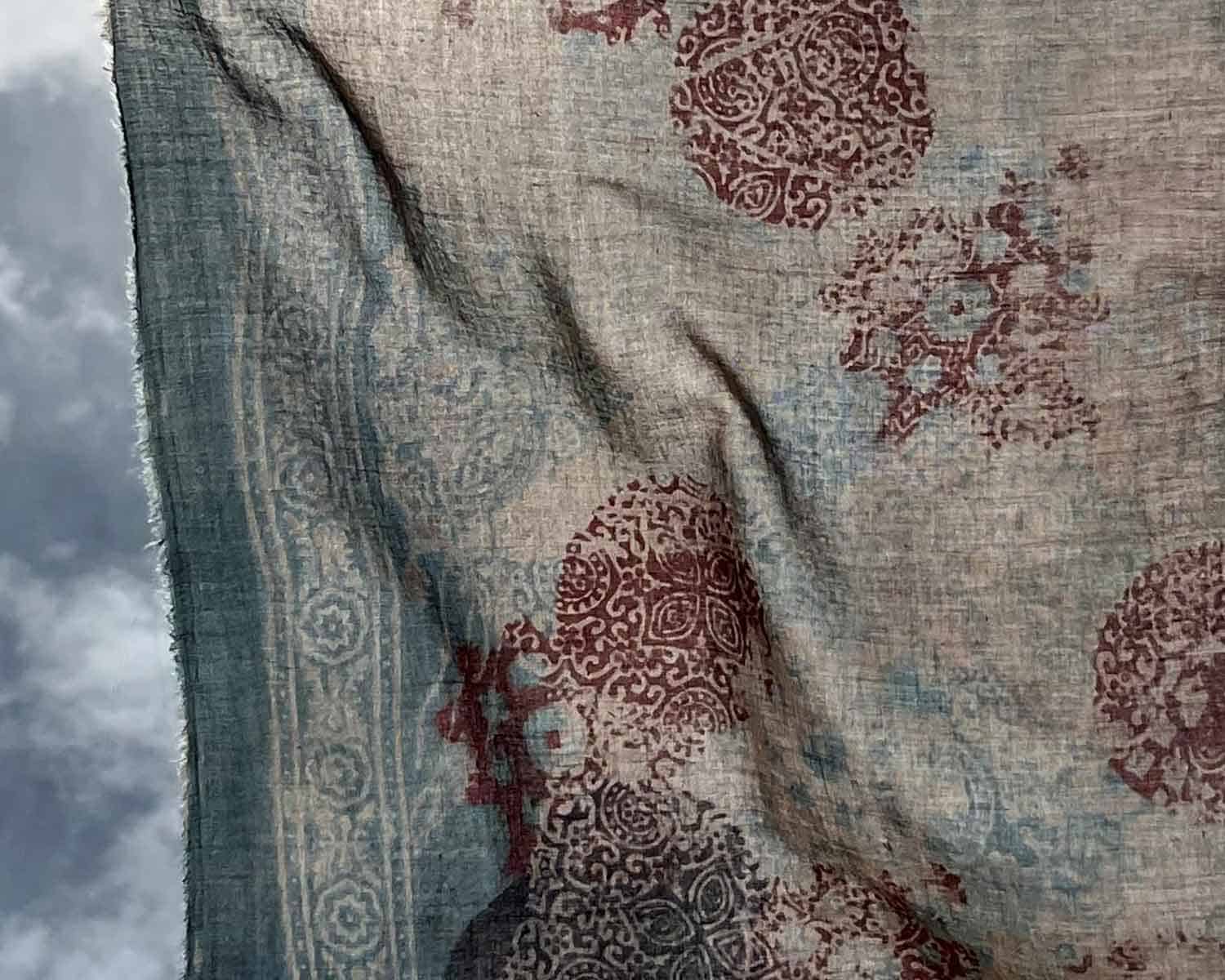
THE Q&A- KNOWING THE UNKNOWN ABOUT AJRAKH:
Q1. Has there been any change or optimization in the sixteen to twenty-three steps process of Ajrakh which is being followed for so many years now?
- This has been the process for generations. No major optimizations can be done in the processes per se. If any step is eliminated, the quality of the craft can get compromised.
Q2. Any technological development that has happened in the above processes?
– No major technological development is there yet in the authentic block printing process. However, people have started using screen-printing and digital-printing to print similar designs.
Q3. What are some of the micro-level challenges that you face as an Ajrakh artisan?
“I enjoy doing what I do”. However, upon pressing our artisan cited the following issues:
- No fans/air conditioners in workshops where Ajrakh printing is done. Having fans would quickly dry up the colours used for block printing. The average temperature is about 44 °C (111 °F) during the hot summer months and can reach highs of 50 °C (122 °F) in villages of Gujarat & Rajasthan. These artisans work in such hot conditions without air conditioners or even fans.
- Marketing: We sell mostly through exhibitions and find it difficult to reach end consumers directly.
- Competition: Artisans typically reside densely in small clusters in only a few villages/towns. There are instances when artisans try to poach each other’s customers through not-so-fair means.
- Unpredictable rainfalls affect the rate of production as after each of the sixteen steps, one needs to spread out and dry the cloth under sunlight. Rain affects the drying process and hence impacts the workshop’s production capacity.
- Water shortage- Water is integral for this craft. With the increasing population and the number of industries around the city going up, the groundwater levels are going down.
Even if artisans get access to water, it’s either saline or rich in iron. Natural dyes do not go well in such water and create blotches on the fabric.
As a result of this issue, a lot of Ajrakh artisans have moved or are gradually moving to synthetic dyes. As far as search for a new source of clean water goes, digging up wells and borewells is not always a guaranteed success and costs heavily on artisans pocket.- Lack of government support – Government projects around finding access to clean water and water recycling units are the need of hour and can help the artisans immensely.
Q5. Can Ajrakh be made using natural dyes only?
- Ajrakh is a block printing technique which can be made on any type of material with both natural as well as synthetic dyes. However, traditionally Ajrakh was made using natural dyes only. With the changing times and availability of resources, artisans moved to synthetic dyes too.
Q6. How much effort does it take to print a saree?
- Get ready for some quick Maths 😉
- A typical Ajrakh block is 6 X 6 inches.
- Which means, in order to print a 1-metre fabric, a block needs to be stamped approx 50 times.
- And for every design there is a set of 3-4 blocks depending upon the # of colours and complexity.
- So in a 4 blocks’ set, for a 1 meter fabric, one needs to stamp approx 200 times.
- This translates to about 1,260 times in a 6.3 metre length saree.
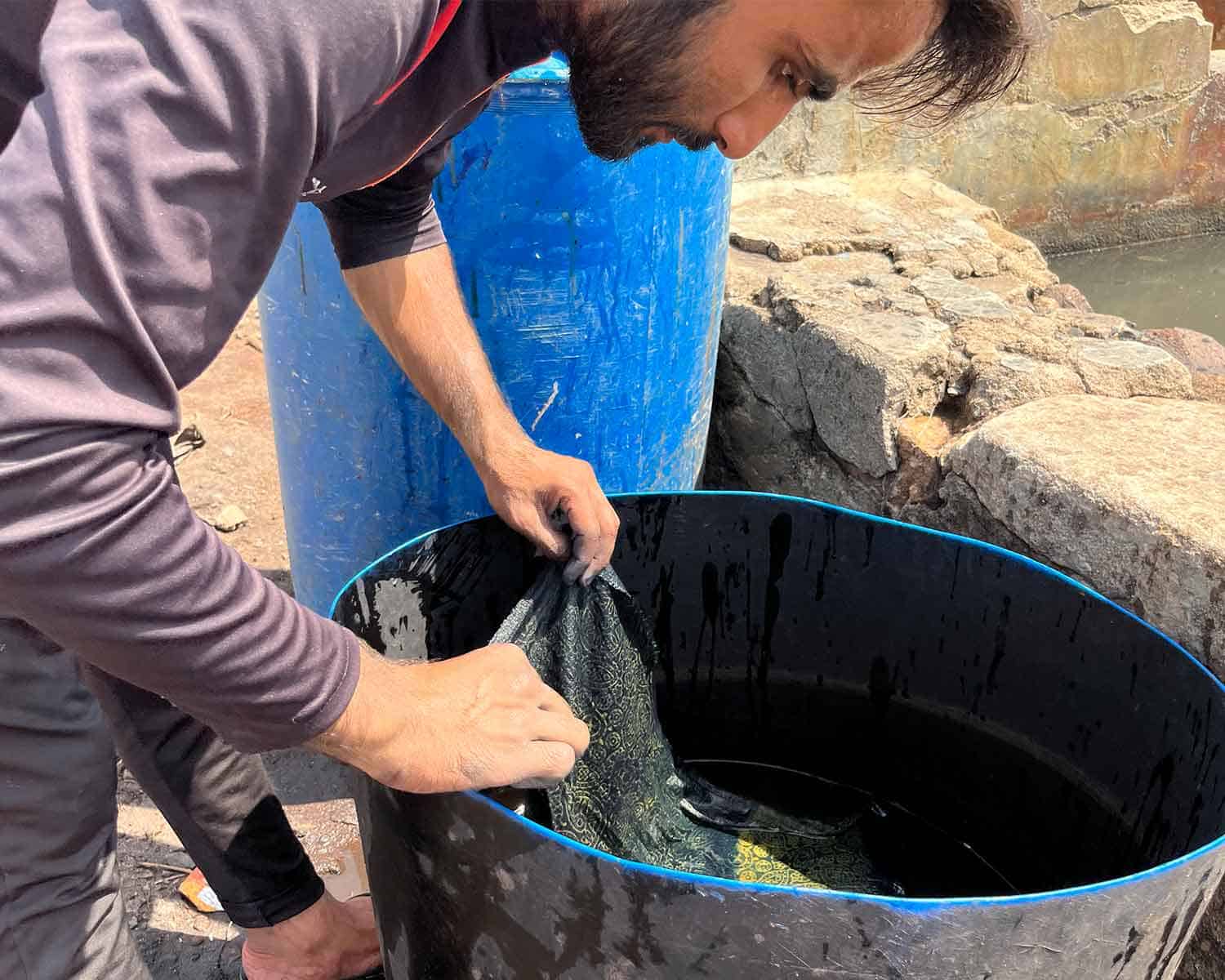
Our visit to the Ajrakh artisans in Gujrat was a great experience as it that gave me a deeper understanding of the intricate art of Ajrakh printing. We were amazed at the level of skill and patience required to create these beautiful designs by hand. We were amazed to see the passion and dedication of the artisans who continue to keep this traditional crart alive since generations. It was truly inspiring to see how they incorporate their own unique styles and interpretations into their work while staying true to the rich heritage of Ajrakh printing. We hope that this article has given you a glimpse into the world of Ajrakh and has sparked your curiosity to explore and appreciate the art of textile printing even further.